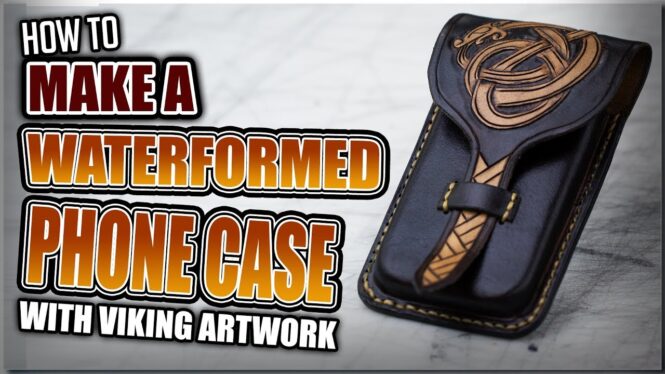
Today I’m going to show you how to
make a custom water formed case. I’m going to be making this case
for my phone… so here we go [Music] before we get started remember that i’ve been
putting both the patterns and artwork for my latest builds on my etsy shop you can find the
link around here somewhere check that out also if you haven’t already make sure you hit the
subscribe button and the notification button so you don’t miss any of my videos so before you
all panic that there’s a piece of wood involved in this build you could water form around your
phone i think overall it would be more difficult maybe wrap your phone and saran wrap it’ll be
hard to keep it in place but you could do it so i’m just showing you the way that i would do it if
i was gonna make a product line so if i was going to make a bunch of phone cases this is how i’d
do it if you want to put saran wrap around your own personal phone and wet mold leather over it
i take no responsibility for anything that might happen to it i don’t think anything well but you
never know and i’m not going to be responsible so while i’ve been rambling we’ve cut out
the phone we’ve sanded it and we’ve sanded it a little more to get a little better shape
so we’ve got a kind of phone case shaped piece now now we’re going to drill some pilot holes so
we don’t split it and then we’re going to screw it into this other piece of wood that gives us a
good base to work off of for molding and why it’s instantly superior to like saran wrapping your
own phone it’s hard to make your own personal phone have a solid place to sit on then we just
shake the leather and that creates water boom so we’re going to mold it around this fake phone
these are a bunch of tools that you could use i specifically like this one i’ve only had it
a little bit but it’s nice and narrow so it’s uh but very smooth and round and it glides
really well so it’s great for molding around edges i like to put these nails right in
the crease you could put them out a little further and avoid the holes i go back later and
try and remove the holes with some burnishing so it kind of it works out i just like how it keeps
it nice and tight to the thing i’m molding around i try and alternate nails and keep it even so
i’m evenly nailing it in a round on both sides obviously the corners are going to be where
it’s the hardest to mold so you’re going to have to work it a little bit make sure you
push it down rub it push it down some more eventually it’ll get to where you want it i see
i’m like really going to town on the corners here also i forgot to mention that when i wet mold
anything i run it under hot tap water first i don’t put it in cold water it’s always hot
tap water it’s not boiling water it’s just hot now that we got that done we’re going to let
it dry we’re just going to speed through the drying process here little time lapse and then
we’re going to start pulling the nails now you can even tell that in the crease it’s still
pretty wet so we have the chance to still mold the holes away once we’ve pulled the
nails so i get most of them most of them get pretty small so we just go around the whole edge
removing nails burnishing and wet molding the edges to get rid of the holes and giving
a little extra once over to make sure our all our parts are smooth and flat
and don’t have a ton of marks on them after we’ve pulled all the nails and done our
burnishing we’re going to let it dry a little longer and then we’re going to line up where
we’re going to use our four hole punch because i’m going to hand stitch this one as well
so i’ve marked where i want my four holes and then i cut it measure it and
cut the other sides i made sure i measured where i was putting the four hole punch
because i don’t want it rubbing on the side of the case when i punch my holes so you don’t
want it too tight you want it a little bit away so that’s pretty good probably could have beveled
the top edge before wet molding it but whatever you don’t need to bevel the sides because once
you stitch it together it’s going to be beveled and burnished as a single piece that’s been put
together you’ll see later now we’re just measuring out our flap it’s a little long i fold it cut
it and then i shape the flap to how i like it draw a little uh little curve it’s a little
big at first so i trim it down slightly and that works for me fire a stitch groove all the
way around the edge so we can line up our holes and then fly through all our holes i use a little
wax there to make the hole punching go quicker and right there i used the four hole punch to measure
the distance and then used a single punch on the corners just to make sure i had it right and
this actually lined up perfect i was pretty happy also you see there that i started at
the top and work down to the corner and then start at the top on the other side
work down in the corner and then did the bottom that helped that just makes sure everything
lines up along the edges for me really well the bottom i could fudge if it was off but i’d
like the edge the two sides to be perfect so both the tongue keeper and the belt loop keeper
are working within how the four hole punch lines up i want a hole on the outside of the keeper
edge to stitch down to the leather as well so you’ll see here there’s four holes on the front
of the pouch but two on the keeper because it’s going to overlap to the edge and stitch down just
looks better and it’s stronger i wasn’t sure if i was going to add a separate tongue because i
liked the idea of how it might uh look when it was stitched on i decided to make it one piece
it’s a lot simpler a little more low profile so i added that on quickly cut out the back and
once the back’s cut out we just need to bevel it [Music] no punch holes well i was close so i’m just marking all the holes because i want
to make sure it’s perfectly lined up then i just do the same thing on the back with the
hole punch and make sure all my holes are the same or close to it then we bevel it and then we’re
going to line up our belt loop keeper on the back and this one’s going to be wider than the keeper
on the front but still it’s going to line up with the four hole punch in mind so there’s the four
holes on the strap itself and then there’s two extra holes on the belt pouch and that allows the
stitch to go off the edge of the loop and stitch down stronger onto the pouch itself so there’s six
holes there this is perfect exactly what i want and then the four hole punch will perfectly line
up across both the top and bottom of that keeper boom done exactly what i wanted fly through some
artwork magically create a serpent really quickly honestly i tried to draw a wolf and i couldn’t
so i went back to a serpent maybe some other time i did a lot of extra stuff on the drawing
itself i’m not gonna carve all the extra tiny little lines i did that you’ll see
here so the same pattern i use on the tongue i use it in the body of the serpent and i
use it on a lot of my serpents it’s just it’s very time consuming so i really
didn’t want to carve all that [Music] once the artwork is all done we’re going to
transfer it onto some tracing film and we’re going to wet our leather and get it onto the leather
once again we’re blowing through this process there’s lots of videos on this we don’t need
to see this in real time [Music] make sure your leather isn’t too wet let it dry a bit
cool to the touch transfer your pattern on and then swivel knife and beveler i didn’t
background at all this time i did once again i did just the beveler around the
edges and it worked really good i really need to practice doing
something other than serpents they look good though this one turned out
well as well so i’m doing something right just need to work on stuff like wolves
ravens bores you know all the favorites then we carefully and tediously paint
with dies and when we’re done painting with the dies we’re going to use the dye to
finish off all the rest of the pouch parts and we’re going to come back and hit the carving
with the finish well finish and resist we’re hitting everything with the finish but we’re going
to use that finish as a resist for the carving and when i get around to the resist i
end up using neutral resolene again it seemed to work really well last time so
i decided to just go with it again here so you don’t make a mess of your edges be sure to
burnish them before you put a finish on so you’re gonna put the wax on burnish there’s a bunch
of different burnishing tools you could use then after that you’re going
to buff out any excess wax or whatever burnishing compound you used and
then after that we can hit it with a finish a spray gun is one of those investments that it
took me a long time to get and it is really well worth the money so if you get a chance to get a
spray gun get a spray gun for your finishes it’s so much easier than streaking it with sponges
and awkward applications put a little too much antique gel on but better better too much
than too little i don’t want it to be uneven i’m being a little messy but uh whatever looks good now it’s on to hand stitching
the uh loops on doing the back it’s pretty straightforward running stitch all the way
down to one in the back and then knot it and we’re going to do this with artificial sinew
on both the belt loop and the tongue loop at the front so a few knots and messy back i should
have dyed that darker but nobody knows but us blow through the stitching here and then the
front of the pouch we’re going to do the same thing running stitch down and back knot it with
the artificial sinew overlapping off of the edge of the keeper so it makes it a little stronger
and looks pretty cool too i like how those look when they’re off like that i’m using four times
the length of the uh holes in artificial sinew and i’m going to this time do a saddle stitch all
the way down to the other end and then tie it off i’m just using two needles and alternating
back and forth all the way around the edge of my project and then when i get to the very
end when i go through the end with the needle i want to go through and come out on the inside
of the pouch and that way i could tie a knot off that’s hidden on the inside of the pouch
you’ll see when i get around the edge here [Music] every three or four holes or so make
sure you’re firmly cinching that uh stitch down so you don’t want any loose stitches because
if you have a loose stitch way back it can be quite a difficult process to make sure it gets
all tightened so here we’re getting to the end and i’m going to stitch up to the very end and
back and then between the two pieces of leather and out on the inside like right here there
we go boom so pull that all the way through and then we’re going to take the other end of
the thread and work its way up and then weave it as well into the inside of the pouch and then
we just need to double knot it and cut it off random note the inside of my pouch is a bit
messy but you can see some wax on the edge so just go make sure you get both sides when you’re
burnishing so i went back and fixed that up later but you don’t notice then i’m using my sander
to get any excess off you could carefully cut it with a knife but it can be tricky so be careful
then we’re gonna bevel it then we’re gonna dye it then we’re going to put wax on it and we’re
going to go over to the burnishing machine which works a lot better for projects
uh parts of the projects like this and make it nice and smooth and
almost look like it’s one piece see it almost looks like one
edge like there’s no seam ah turned out pretty good if you enjoyed this
video make sure you give it a thumbs up hit the notification button so you don’t miss
any future videos and check out my etsy for both patterns and artwork and until next time
keep on being creative in whatever it is you do