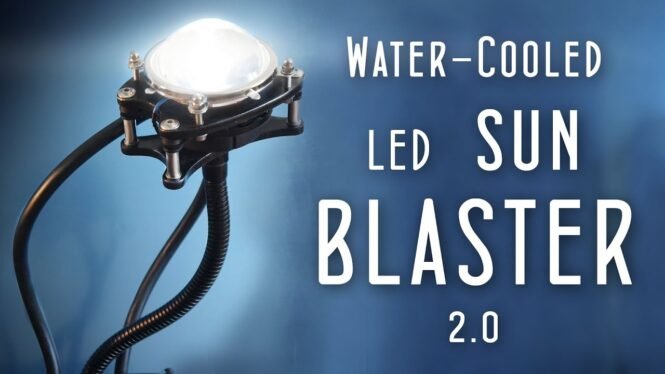
In this video we're going to create an incredibly
bright watercooled led light that not only looks really awesome, but is also extremely
versatile. Its versatility is thanks to the use of liquid cooling to take the heat away
from the LED, as it allows the light to be angled into a variety of different positions.
Another great feature of this light is that we'll be using an LED that looks literally
identical to sunlight. Seriously, this thing is amazing – there have been several times
where I've used it on a cloudy day and have later been subconciously convinced that the
sun's come out and is streaming through the window.
Seriously, it's crazy.
This also makes it suitable for video and photography work, as colours are absolutely
spot on. It even allowed me to get this really awesome timelapse, as the daisies too were
convinced that it was actually sunlight. Although this build is a little bit on the
expensive side compared to what I usually do, it's quickly risen to one of my favourite
and most used DIY Perks projects as it provides something very unique, and is a genuinely
useful tool to have. The build process too is particularly interesting,
especially when we get to making the custom brackets for the head, but before we begin
I just want to give a quick shoutout to VideoBlocks, who are kindly sponsoring this video.
If you've
not heard of them before, they are a stock footage company offering not only stock footage but
also after effects templates, background plates, and more. They're perfect for YouTubers as
an entire years access to their whole library is just $99, which is really affordable, and
on top of that they're currently offering a one-week free trial with which you can download
up to 140 clips, which is a great way to explore what they offer and you get to keep them afterwards
which is fantastic. So if that sounds good to you, free to sign up at videoblocks.com/youtube
or by following the link in the description. Right so, let's get on with building this
light. The first thing we'll need is obviously the
liquid cooler itself. These are usually used for cooling high end computer processors,
and you can find a link the one I used in the description.
We'll be mounting it to a custom frame, for which we'll need a 1 meter length of angled
aluminium.
The back of the cooler can then be placed
at the middle of this length, and then a knife used to mark the position of its outer edges.
We can then make some 90 degree V marks at these points like so, and then use a hack
saw to carefully cut them out. Once they're both cut it's then just a case
of bending them both into 90 degree angles, after which the frame should match the width
of the radiator. To make the legs, the same can be done again,
with one V at the end of the radiator and the other about 6cm further along.
These can again be bent into 90 degree angles, after which it should look something like
this. As you can see, on the feet I have cut one
side of the angle off entirely – this basically means that when the light is completed the
feet can be slid underneath objects on a shelf, meaning you can get it at a high lighting
angle without resorting to a mount of some kind. It does make the legs less rigid though,
and means that the light is a bit less stable, so if you don't want to mount the light underneath
a shelf, I do recommend that you leave this step out.
In any case, before we attach the cooler to it we need to sort out the LED power circuitry.
As the LED we'll be using requires about 30v, we need to use a voltage booster.
This basically
takes a lower voltage and steps it up depending on the value of the indicated variable resistor,
which you can adjust yourself. This not only allows us to use a variety of power sources
to power the light, but also means that we can add a knob that allows us to easily adjust
the brightness of the LED. This board also has the ability to limit current,
which is essential if you want to get the most out of these high power LEDs while protecting
their longevity. As these boards are a little hard to find, I have as usual placed international
purchasing links in the description. So the first thing we'll need to add is the
aforementioned brightness knob. We'll start by scraping off the glue around the base of
the innermost variable resistor, and then bend it back and forth until it breaks free.
Some of you may want to desolder it instead, but as we won't be needing it again it's much
easier to just take advantage of metal fatigue.
After removing as much of the remaining glue
as possible, we can solder three extension wires to the outermost of the three solder
pads. We now need two new variable resistors and
also a linear potentiometer, all with a value of 2kohms. These need to then be soldered
to the extension wires as shown in this circuit diagram.
We'll be using the two blue variable resistors to adjust the minimum and maximum brightness
points later on in the build, but for now we'll get started on making the platform that
the voltage booster will be mounted to.
So we'll get some short lengths of aluminium
angle and round off their corners with a file so that they fit snugly inside the front of
our frame. As these will later be screwed together, we
need to drill some holes through them both. Thanks to the three points of contact, they
will make the frame much more rigid. So we'll just unscrew them again for now,
as it's time to work on the platform itself. To make it we'll first need to cut a rectangle
out of some thin aluminium sheeting, after which we can drill some holes through our
short supports into it so that we can again screw them together later.
Next we can place our voltage booster on the rectangle, and use a sharp point to mark out
its mounting hole positions.
We'll also need to mark the point directly underneath the
variable resistor so that we can adjust the output current later.
Once these are drilled through, we can make two more larger holes adjacent to them – one
for the potentiometer to fit through, and the other for a power switch.
After the supports have be screwed on with some screws and nuts, it should look something
like this, and the last thing to do is get some 15mm long PCB standoffs and securely
mount them to the back like so. These standoffs will allow us to later attach
the voltage booster with the component side facing inwards, which will not only protect
it, but also expose the bottom side of the voltage booster to the airflow from the radiator's
fan, which will keep it nice and cool. Now we can screw our platform to the frame,
after which it should look something like this.
Now as we'll later be using a microphone goose neck to support the LED, we need to make a
mount with which we can later fix it to the frame with.
These goose necks use a fairly uncommon thread, so what we'll need first is an adapter that
converts it into a standard one quarter inch UNC thread instead.
Now we can get a small piece of aluminium angle and drill a hole in one side, gradually
making it larger until the adapter can be pushed through.
This can then be mounted to
the back of the frame using screws and nuts. Now it's time to make the holes through which
we'll attach the radiator. As the radiator has four fan holes on its top and bottom,
we'll use the included fan as a template to mark where these holes should be on the frame.
Whilst we've got the drill out we might as well drill two pairs of holes on the side
and back.
These will be used with cable ties to later hold some wires in place.
Now we can add our electronics, starting with the power switch.
A short length of wire needs to be soldered to one of its tabs, after which it can be
inserted through the hole we made earlier. Now we can add the input power connector,
which is just a short length of wire with an XT60 socket soldered to the end. This needs
to be soldered to the power input of the voltage booster, with the positive wire going through
the switch. As you can see, I've also soldered two extra black wires to the input, which
will later be used to power the pump and fan. Now we need to get some more wire – I'm using
an old mains cables here by the way – and solder one end of it to the power output on
the voltage booster. We can now screw the voltage booster to the
standoffs we added earlier, and after trimming off the unused legs on the variable resistors,
we can mount our potentiometer as well, finishing it off by adding a knob.
Now we can use some cable ties through those holes we made earlier to hold the wires in
place, after which we can finally attach the radiator using its included screws.
Now things are going to get pretty interesting as we're reaching the final stages.
As I mentioned earlier we're using a microphone
goose neck to support the LED. It's perfect as it can be bent into different positions
and stay there, but it's also hollow, which means we can keep things neat by routing the
wires down inside it. The problem is that when we add our thread
adapter one end gets blocked up, so what we'll do is drill three holes in the side of the
base for the wires to enter through instead. We'll start with the LED's power wires, which
are hooked up to the output of the voltage booster. Now a piece of stiff steel cable
can be pushed through from the other side of the gooseneck and clamped down onto the
wire.
The whole thing can then be pulled back through the neck, taking the wire with it.
Now you may have noticed the little green wire. It has two cores inside, and is there
to later carry power to the pump, which resides in the cooling pad.
Now that's done we can attach the gooseneck to the frame using the thread adapter and
a quarter inch UNC nut. Now it's time to start my favourite part of
this build, which is to make the head. It's essentially a custom bracket for the cooling
pad, and actually makes the head look quite cool.
To make it, we'll start by printing off the template I have included in the description
– it needs to be printed without any scaling, and you can use the included measuring box
to make sure it's printed at the right size.
These templates need to be then stuck onto
some 6mm thick MDF using double sided tape. You don't have to use MDF, but it is the most
practical option for most people as it's easy to cut yet sturdy enough for this application.
Notice that there are coloured dots on each shape – these mark the hole points that need
to be drilled through, and you can see the required bit size by referring to the included
key. A coping saw can then be used to carefully
cut out the shapes, and after giving them a good sanding down you should end up with
something like this. Notice that the smaller bracket has a countersunk
hole in the middle.
This is because we'll be using another thread adapter on the gooseneck
to attach it to the brackets later. Having it countersunk allows its thread to be exposed
as it's not quite tall enough to just reach through the MDF on its own. The easiest way
to make this countersink is by using a spade bit.
Now that both brackets have been cut it's time to prepare them for spraying by giving
them at least five thin layers of undercoat. This undercoat can then by sanded down using
some fine grit sandpaper until it's almost plastic like in appearance.
They can now be sprayed with whatever colour you like. I went with a black satin finish
as it gives the appearance of some kind of painted metal, and looks pretty good I'd say!
So now we need four 20mm long threaded rod connectors, four 12mm long flanged head screws,
and four washers, all of which need to be M5.
After inserting our goose neck adapter into the smaller bracket, we can thread our screws
through from the other side, add a washer, and then screw on the rod connectors.
Next we need to push our wires through the hole, and screw the bracket tightly to the
goose neck.
This gives us a fantastic mount to which we can attach the rest of the head.
The next thing we can do is wire up the pump that's in the cooling pad. The connector it
uses is a standard computer fan connector, where the middle wire is positive, and the
wire marked with a 1 is negative. This connector needs to be chopped off and the wires then
soldered to the green dual core wire that I mentioned earlier.
Any excess can be pulled down inside the gooseneck to keep things neat.
The liquid cooler comes with mounting hardware for both AMD and Intel processors – as our
DIY brackets have been designed for the AMD hardware, we'll get the AMD brackets and insert
the included plastic retainers into its holes like so.
Now what we need to do is get four more flange head M5 screws, this time 25mm long, and push
them through the large holes on our other MDF bracket, which can then be inserted through
the AMD bracket.
To pull the plastic tabs into the holes on
the MDF, we can squeeze them together using a wingnut. It's quite a tight fit but it does
do the trick. The whole thing can then be locked into the
notches on the cooling pad, and then tightly screwed to the rod connectors using an allen
key. It should now look something like this, and it's finally time to add the LED.
Pretty much any similar style 100w LED emitter can be used here, but for the best results
I highly recommend the ones made by Yuji LED, as they have absolutely fantastic colour rendition.
They are more expensive than the cheap ones you can get from places like eBay, but as
I found out in a previous video they are well worth the extra, and I can't recommend them
enough.
To mount the LED it's just a case of pushing
it down onto the pre-applied paste on the cooling pad, and then soldering the power
wires to it. Make sure that you get the polarity correct though as it won't light up otherwise.
Now we need to add a lens to focus the light forwards. As you can see this thing is huge,
and as it's designed specifically for these LEDs it comes with a suitable reflector and
mounting bracket. You can find a link to it in the description.
The reflector has four little prongs on the bottom, which can be inserted into the matching
holes already present on the LED. Once that's done we can place the lens on
top following it up with the bracket. Now we need four 25mm long M4 screws with
accompanying dome nuts and washers, which can be used to clamp the lens and reflector
in place. Now we can add the fan. As I mentioned earlier
this came with the liquid cooler, and it's just a case of using the included screws to
attach it to the radiator.
I am however using an extra fan grille as it will protect the
blades if something were to touch them. Looking good!
So now the last thing to do is sort out the power source for both the fan and pump.
What we'll use for this is a little voltage regulator. This works similarly to the voltage
booster we're using to power the LED, only this one is much less powerful and actually
reduces the voltage rather that boosting it. So after setting it to output 12v, we can
solder the input pads to those additional wires we added to the bigger voltage booster
earlier.
To its output pads we can then solder the
pump and fan. The pinout for the fan by the way can be found in the description.
We can now glue it to the frame with a piece of cork in between to act as an insulator,
and with that the light is pretty much complete. But, before we power it on we need to calibrate
our power circuitry so that the LED is driven with the perfect amount of current.
To do this is really simple, and we'll start by cutting through the positive wire that
goes to the LED. I know, we literally just put this thing together and we're already
cutting it up, but it's the only way to check the LED's current properly as it does need
to be cooled at the same time. We can then hook these wires up to a multimeter
so that the current flows through the multimeter rather than directly going to the LED.
Now we can insert a little screwdriver into that hole we made earlier on our voltage booster
platform use it to twist the remaining variable resistor on the voltage booster fully clockwise.
You should hear a little click click on every full turn once it's at its maximum.
We can do the same to both of our extra variable resistors that we added earlier, but this
time they need to be adjusted fully anti-clockwise We're now ready to power on the LED for the
first time, but before we do that we obviously need a power source.
The light accepts a DC current rated at anything between 12 and 24v, which allows you to use
anything from an old laptop adapter to a car battery.
The only requirement is that it needs
to comfortably provide at least 110w. I'm going to use an old printer power brick
that outputs 8A at 15v, meaning that it can supply 120w, which is perfect for the LED.
As it had a proprietary connector on the output side, I chopped it off and replaced it with
an XT60 connector instead. After plugging it into the light and turning
on the power switch, the fan and pump will fire up, as will the LED. You should hear
a sort of bubbly noise at first as well from the pump – this is normal and it's a good
indicator of it all working properly, and it will quieten down after a minute.
The multimeter's display should be telling you that the LED is drawing about 1A, and
at the moment turning the brightness knob shouldn't really do anything.
So, we'll make sure that the brightness knob is at its maximum, and then slowly turn the
variable resistor on the voltage booster anti-clockwise.
You should start to see the LED increase in
brightness, and the multimeter should show an increase in current as you go. You need
to keep going until the multimeter registers 3A, as this is the maximum that the LED is
rated for. Now with the maximum current limited to 3A,
we can adjust the output voltage range so that the LED dims properly when our brightness
knob is adjusted. With the brightness knob still set at its
maximum point, we'll grab the variable resistor that's wired up in series with the potentiometer
and adjust it clockwise until the current starts to dip. We'll then backtrack slightly
until it starts to level off. We want to get it as close to this levelling off point as
possible, so it may be necessary to backtrack back and forth until you get it right.
Now we can turn the brightness knob to its minimum value, and then grab the other preset
– the one that's connected to the potentiometer in parallel, and then begin turning it clockwise.
The multimeter should show the current dropping as you do this, and the LED will decrease
in brightness accordingly.
This variable resistor basically sets the minimum brightness level
of the LED, so you can adjust it to your personal preference. I adjusted mine so it was just
slightly glowing. Once you're happy the variable resistors can
be tucked away under the radiator. The knob should now smoothly adjust the brightness
from maximum to minimum, with the current itself capping itself at 3A.
Now all we've got to do is re-attach our cut wire, making it look neat by using some heatshrink.
See, that cut wasn't so bad after all was it?
And with that, the light is complete and looking awesome!
Now before we wrap this up it's worth noting that it's also pretty easy to make a wall
mount for it. This can be made by chopping off the outer
edges on a piece of angled aluminium, which can then be screwed to a wall. The light's
legs can then be hooked under it, allowing it to quickly become a pretty interesting
looking lighting fixture. Right so I hope you've enjoyed this video.
It was really hard to make due to its length – it took quite a long time – but I'm really
happy with the project, as I built it in December and I've used it in every video I've made
since then so it's been actually a genuinely useful production tool.
I didn't really cover
the brightness of this in the video, but it's ridiculously bright – brighter than the 100w
flashlight I made a while ago, which was equivalent to about 1000w if it was an incandescent lightbulb
– and that's because the LED is more efficient because it's a Yuji LED and they're much better
quality. I would like to make a bigger version of this,
still using watercooling, kind of quite eccentric perhaps, with maybe 10 LEDs, but I might need
Yuji's help for that as they are relatively expensive LEDs so Yuji if you're watching
I would really like to pursue this so send an email or something if you're interested.
Right so I think that's it for this video, I've got some really exciting ones coming
up in the next few months, so stay tuned for those, but other than that I will see you
in the next video.
Goodbye for now! If you'd like to see another of my projects,
then why not check out this one in which I show you how to make some really beautiful
mushroom lights. Alternatively, if music is more your thing, then what about making a
unique concrete volume knob to bring back that analogue feel to your audio? They're
both worth a watch, so I hope you enjoy them!.